Why active cooling
Active cooling is a better and cost-effective alternative to passive cooling. The best passive cooling material is diamond with a thermal conductivity of 2200 W/(m.K).
However, this material is costly and difficult to machine to the dimensions required by the package. The best passive cooling metal is silver with a thermal conductivity of 420 W/(m.K), closely followed by copper at around 400 W/(m.K). Active coolers have demonstrated thermal conductivity values of more than 1000 W/(m.K).
Active cooling can be either one-phase or two-phase. In one-phase active cooling, the liquid being pumped around is never allowed to boil, such as is the case in a car engine. In a two-phase active cooling, a part of the liquid vaporizes so that both a liquid and a gas phase of the fluid are present in the cooling system. The fact that most liquids have a large latent heat of vaporization means that the vapor contains a large amount of heat. Moving the vapor to the cold side of the system and letting it condensate there implies the movement of a large amount of heat from the source to the sink.
The volume of the liquid in a two-phase cooling system expands greatly when it vaporizes. This increases the pressure locally, which can be used to circulate the fluid in the cooling system, so that no external pumping is required.
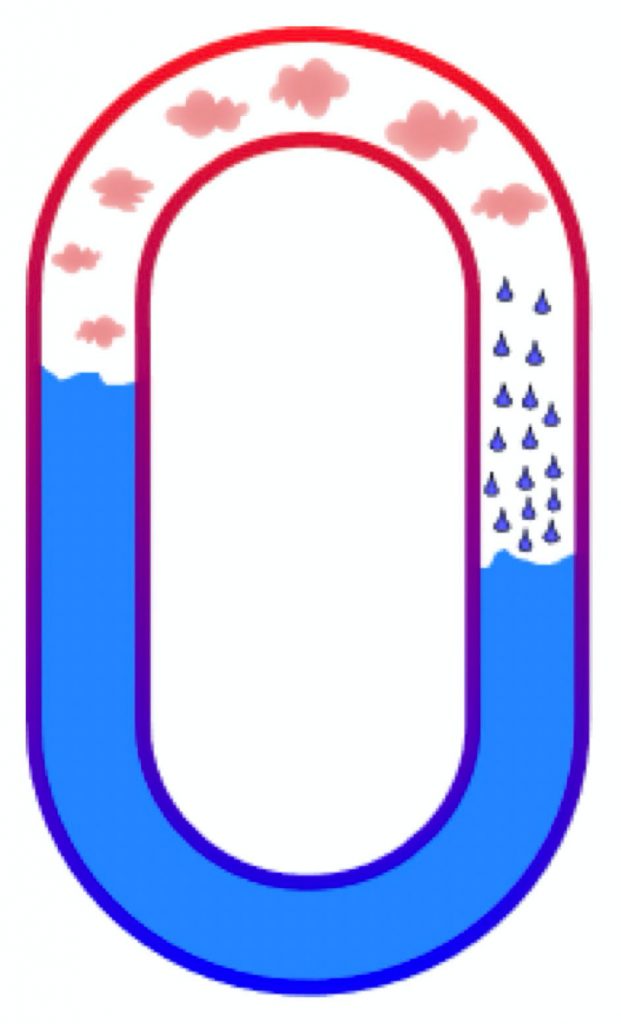
When the heat pipe is laid in the form of a serpentine that crosses the hot and cold regions multiple times, the movement of the vapor in the heat pipes is oscillatory. Vapor bubbles move back and forth in the serpentine while growing in the hot zones and diminishing in the cold ones. These oscillatory heat pipes have a very effective cooling performance.
When alternating the diameters of the heat pipes in each branch of the serpentine, the oscillatory movement becomes less dependent on the orientation of the gravity. This type of oscillatory heat pipes also work under low-gravity conditions and can be used in space.
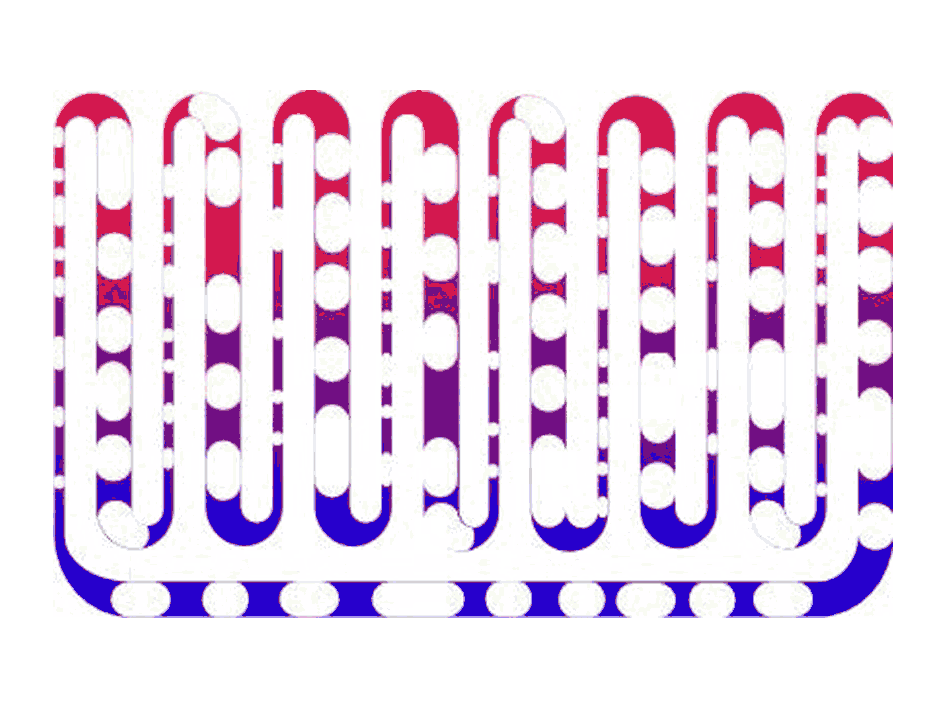